A Comprehensive Guide to the Process and Advantages of Plastic Extrusion
In the huge realm of production, plastic extrusion emerges as a highly reliable and necessary procedure. Transmuting raw plastic into continuous accounts, it satisfies a variety of sectors with its remarkable adaptability. This guide intends to elucidate the complex actions involved in this approach, the kinds of plastic suitable for extrusion, and the game-changing benefits it offers the market. The ensuing discussion assures to unravel the real-world effects of this transformative procedure.
Recognizing the Essentials of Plastic Extrusion
While it might show up complex in the beginning look, the process of plastic extrusion is essentially basic - plastic extrusion. It is a high-volume manufacturing method in which raw plastic is melted and formed right into a continuous account. The procedure begins with the feeding of plastic product, in the kind of pellets, granules, or powders, into a heated barrel. The plastic is after that thawed utilizing a mix of warm and shear, applied by a turning screw. As soon as the molten plastic gets to completion of the barrel, it is compelled via a small opening called a die, forming it into a desired kind. The shaped plastic is then cooled, solidified, and reduced right into preferred lengths, completing the process.
The Technical Process of Plastic Extrusion Explained
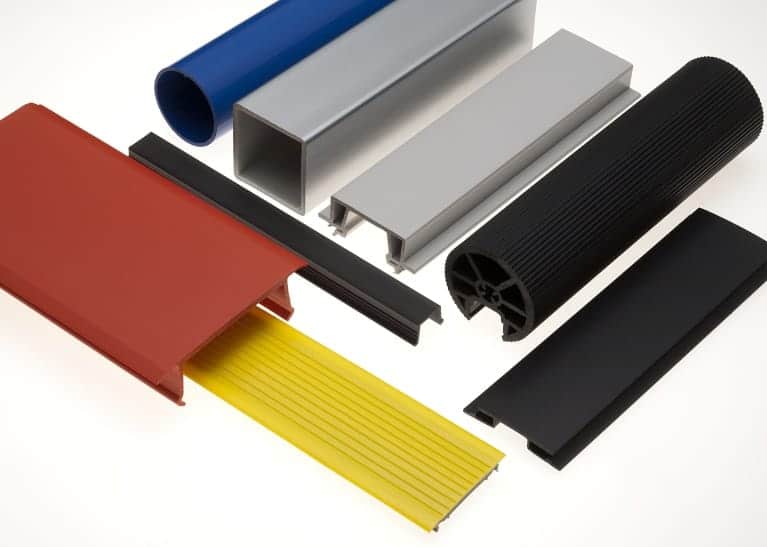
Kinds Of Plastic Suitable for Extrusion
The choice of the best kind of plastic is a vital aspect of the extrusion procedure. Different plastics provide distinct residential or commercial properties, making them more fit to certain applications. Recognizing these plastic types can considerably enhance the extrusion process.
Comparing Plastic Extrusion to Various Other Plastic Forming Methods
Recognizing the sorts of plastic suitable for extrusion leads the way for a wider conversation on exactly how plastic extrusion stacks up versus various other plastic creating approaches. These consist of injection molding, strike molding, and thermoforming. Each method has its unique uses and advantages. Shot molding, for circumstances, is excellent for creating complex components, while strike molding is excellent for hollow items like containers. Thermoforming excels at developing shallow or big parts. Nonetheless, plastic extrusion is unparalleled when it involves producing continuous profiles, such as seals, gaskets, and pipes. It also enables for a regular cross-section along the size of the product. Thus, the selection of technique mostly depends upon the end-product requirements and specs.
Trick Benefits of Plastic Extrusion in Manufacturing
In the realm of manufacturing, plastic extrusion offers numerous considerable navigate here advantages. One noteworthy advantage is the cost-effectiveness of the process, which makes it an economically attractive production technique. Furthermore, this strategy gives premium product flexibility and enhanced production rate, thereby boosting total manufacturing performance.
Economical Production Method
Plastic extrusion leaps to the forefront as a cost-effective production approach in production. This process stands apart for its ability to generate high quantities of material rapidly and efficiently, giving makers with significant savings. The main cost benefit is the capability to make use of cheaper resources. Extrusion uses thermoplastic products, which are less expensive contrasted to metals or porcelains. Even more, the extrusion procedure itself is relatively straightforward, minimizing labor costs. In addition, plastic extrusion requires less power than standard production methods, adding to lower operational expenses. The procedure additionally reduces waste, as any type of excess or malfunctioning materials can be recycled and reused, supplying an additional layer of cost-effectiveness. Overall, the monetary advantages make plastic extrusion a highly eye-catching choice in the production sector.
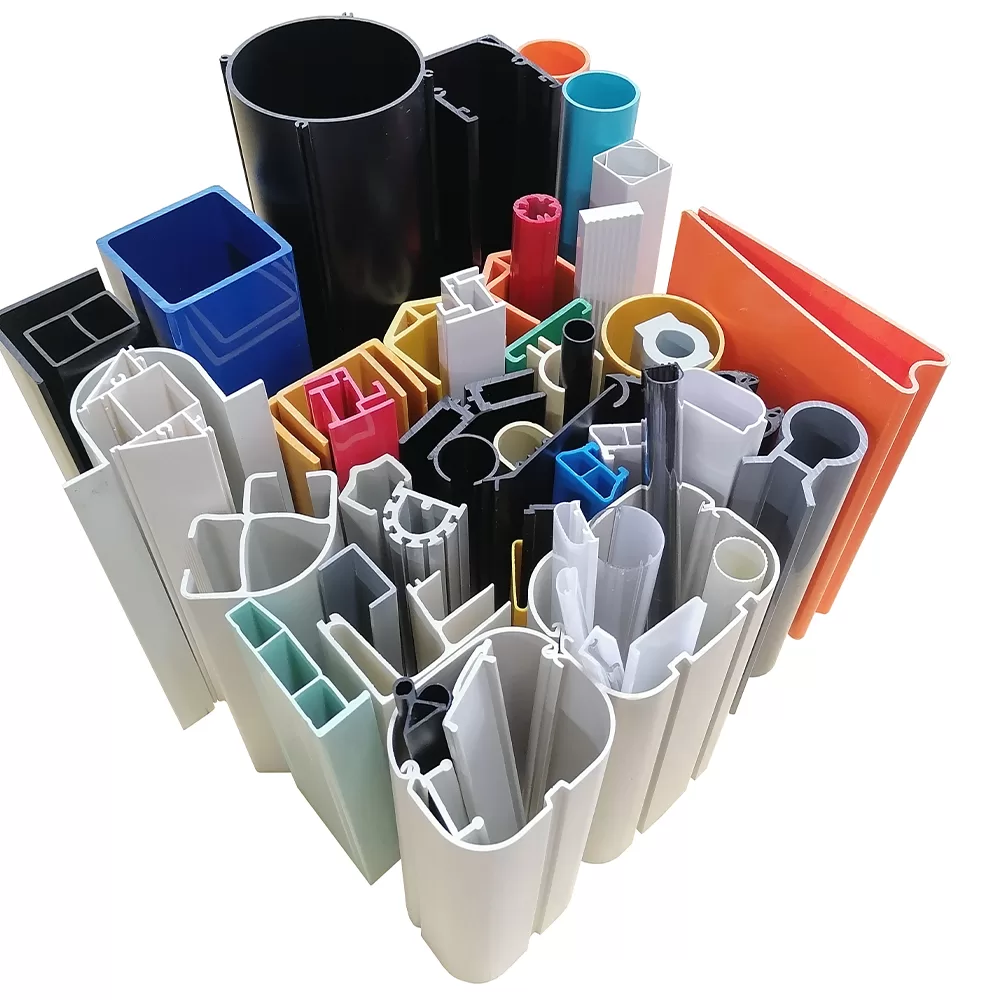
Superior Product Adaptability
Past the cost-effectiveness of plastic extrusion, one more considerable advantage in manufacturing hinge on its premium item versatility. This procedure permits the development of a broad array of items with varying sizes, layouts, and shapes, from basic plastic sheets to complex accounts. The adaptability is credited to the extrusion die, which can be customized to produce the wanted item style. This makes plastic extrusion an optimal option for industries that call for personalized plastic components, such as auto, building and construction, and product packaging. The ability to generate varied products is not just useful in meeting specific market demands yet additionally in enabling suppliers to explore new item lines with marginal capital financial investment. Fundamentally, plastic extrusion's item flexibility cultivates advancement while enhancing functional performance.
Improved Manufacturing Rate
A significant advantage of plastic extrusion exists in its improved production speed. Few other manufacturing procedures can match the rate of plastic extrusion. In addition, the capacity to keep constant high-speed production without giving up item top quality establishes plastic extrusion apart from various other techniques.
Real-world Applications and Impacts of Plastic Extrusion
In the realm of production, the technique of plastic extrusion holds extensive importance. The financial advantage of plastic extrusion, largely its More about the author economical and high-volume output, has revolutionized manufacturing. The market is constantly aiming for technologies in naturally degradable and recyclable materials, suggesting a future where the benefits of plastic extrusion can be kept without endangering ecological sustainability.
Conclusion
Finally, plastic extrusion is a extremely efficient and efficient method of transforming resources right into varied products. It offers numerous benefits over various other plastic developing methods, including cost-effectiveness, high result, marginal waste, and style adaptability. Its influence is exceptionally felt in various sectors such as building and construction, vehicle, and consumer goods, making it a pivotal sites procedure in today's manufacturing landscape.
Delving deeper right into the technical process of plastic extrusion, it starts with the choice of the appropriate plastic product. When cooled, the plastic is cut into the called for sizes or injury onto reels if the product is a plastic movie or sheet - plastic extrusion. Comparing Plastic Extrusion to Other Plastic Forming Methods
Understanding the types of plastic appropriate for extrusion paves the method for a wider discussion on just how plastic extrusion piles up versus other plastic forming methods. Couple of various other production procedures can match the rate of plastic extrusion.